Wie funktioniert das Kaltgasspritzen?

Kaltgasspritzen ist das modernste Verfahren im Bereich des thermischen Spritzens

Im Vergleich zu den herkömmlichen Verfahren bietet das Kaltgasspritzen besondere Vorteile, da der Spritzwerkstoff beim Prozess weder an- noch aufgeschmolzen wird. Dadurch ergibt sich ein breiteres und flexibleres Einsatzspektrum als bei anderen thermischen Prozessen.
Die hohe kinetische Energie der Partikel und der damit verbundene hohe Verformungsgrad beim Aufprall auf dem Bauteil ermöglichen die Herstellung von homogenen und sehr dichten Schichten - bei einer variablen Schichtdicke von wenigen hundertstel Millimetern bis hin zu mehreren Zentimetern.
Es werden vorwiegend metallische Schichten hergestellt, deren physikalische und chemische Eigenschaften sich kaum von denen des Ausgangswerkstoffes unterscheiden.
Bei der neusten Anlagentechnologie der Impact Innovations GmbH wird ein Prozessgas, vorzugsweise Stickstoff oder Helium, bei bis zu 50 bar Druck einer Spritzpistole zugeführt und im Pistolengehäuse auf maximale Temperaturen von bis zu 1100°C aufgeheizt.
Die anschließende Expansion des erhitzten und hochgespannten Gases in einer konvergent-divergenten Düse auf Umgebungsdruck hat zur Folge, dass das Prozessgas auf Überschallgeschwindigkeit beschleunigt und im gleichen Moment auf Temperaturen von unter 100°C abkühlt.
Das Spritzpulver wird mittels einer Pulverförder-Einheit und einem gleichartigen Trägergas im konvergenten Bereich der Düse injiziert und im Hauptgasstrom auf Partikelgeschwindigkeiten von bis zu 1200 m/s beschleunigt.
Die Partikel treffen in dem stark fokussierten Spritzstrahl auf die (in vielen Fällen unbehandelte) Bauteiloberfläche auf, verformen zugleich das Substrat und sich selbst und bilden eine fest haftende, dichte und oxid-arme Schicht.
Erfahren Sie mehr über Kaltgasspritzen in diesem Video:

Partikelgeschwindigkeit als Maß für Schichtqualität und Effizienz beim Kaltgasspritzen
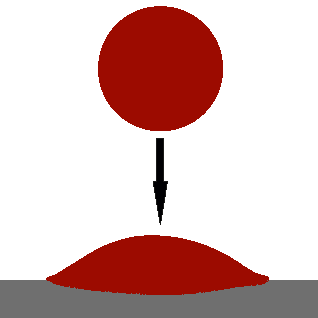
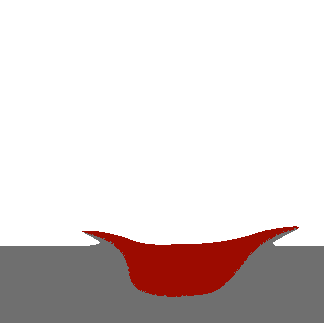
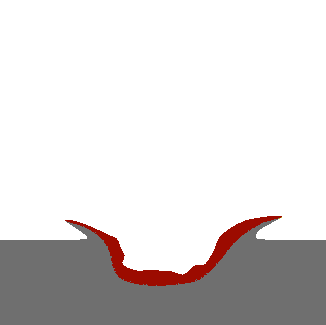
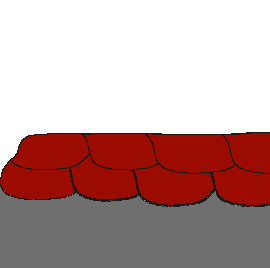
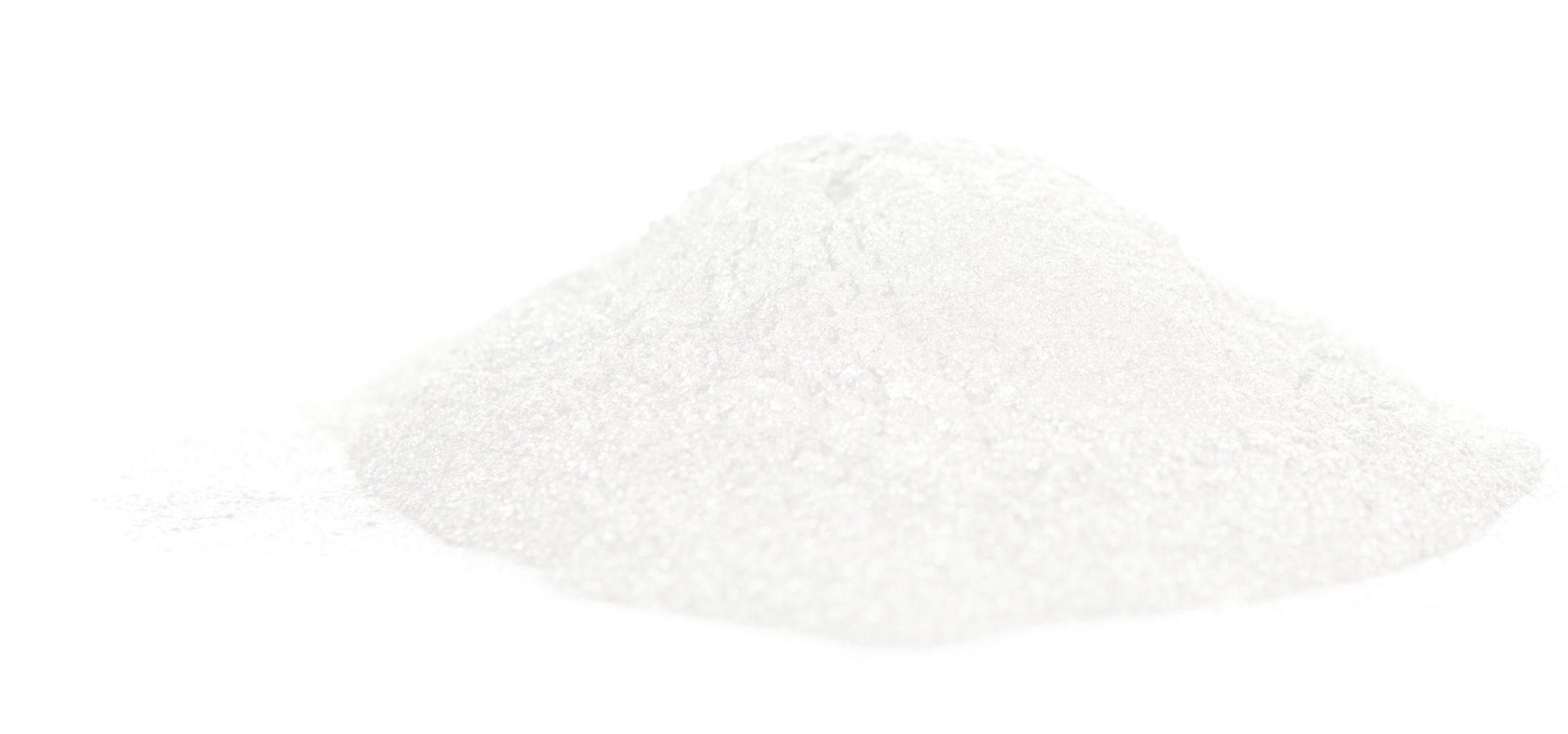
Welche Werkstoffe lassen sich mit Kaltgas-Anlagen verarbeiten und was kann man beschichten?
Individuelle Verarbeitung