Manufacturing Rocket Combustion Chambers with Cold Spray

Cold spraying is an economical technique used to repair and restore industrial products by replacing damaged parts. The characteristics of cold spraying, which involve depositing materials in a solid state, render it an appealing method for repair and restoration.
This approach preserves the distinctive properties of the original components while also enhancing the properties of the repaired elements through the deposition of essential materials.
The production of intricate components like combustion chambers is streamlined through the utilization of cold spraying.
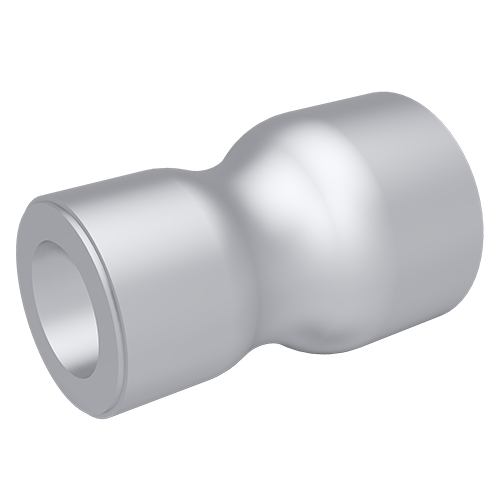
Substrate preparation
In Cold Spray Additive Manufacturing, the deposition of the chosen material onto a mandrel (substrate) is a crucial step. Aluminum alloys are commonly the preferred choice for mandrel materials in additive manufacturing applications. The exterior form of the mandrel must accurately replicate the internal shape of the intended combustion chamber.
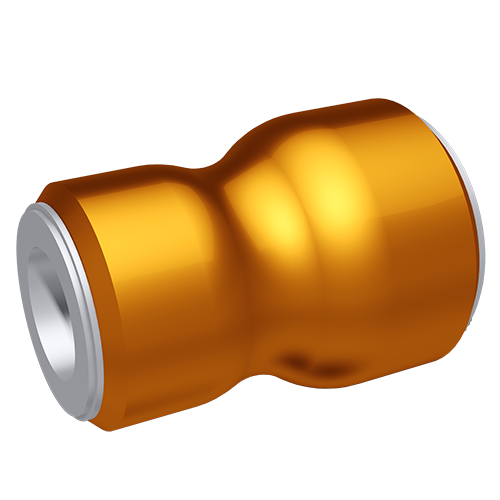
Cold Spray deposition of the Cu alloy liner
The designated copper alloy is applied through Cold Spray deposition onto the designated area, ensuring the attainment of the desired shape and dimensions.
Utilizing the Impact Cold Spray System EvoCSII 5/11, the deposition rate for copper alloys can reach up to 12 kg/h.
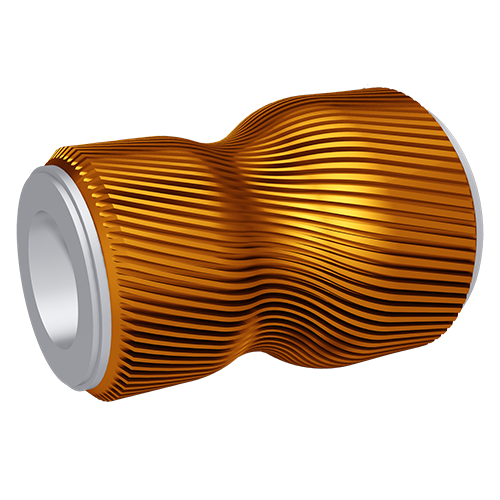
Subtractive cooling channel formation
After the deposited material attains the necessary thickness, the Cold Spray additive process is halted, making way for the subsequent subtractive process.
The surface of the deposit is milled to achieve the desired shape, and the cooling channel grooves are also milled into the deposited material.
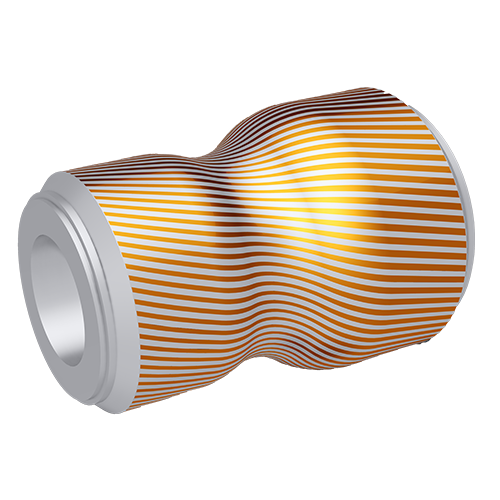
Filling the channels
Following the creation of the open cooling channels through milling, the channel grooves are filled with dissolvable material using the Cold Spray Additive Manufacturing process. For filler material, pure metals or alloys that can be chemically dissolved are employed.
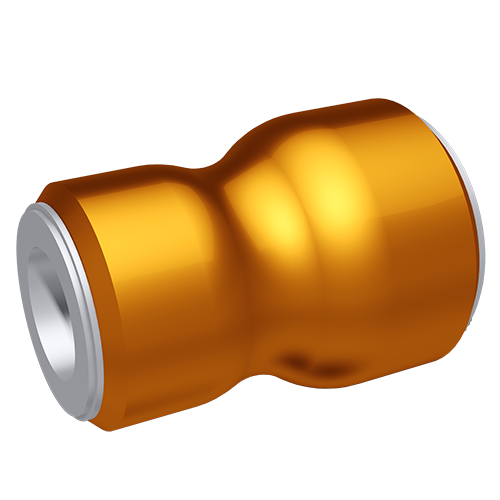
Closing the channels
The Cold Spray deposition process then proceeds atop the filled grooves, covering the cooling channels and achieving the necessary thickness for the intended combustion chamber design. To seal the channels, either identical or different copper alloys are utilized.
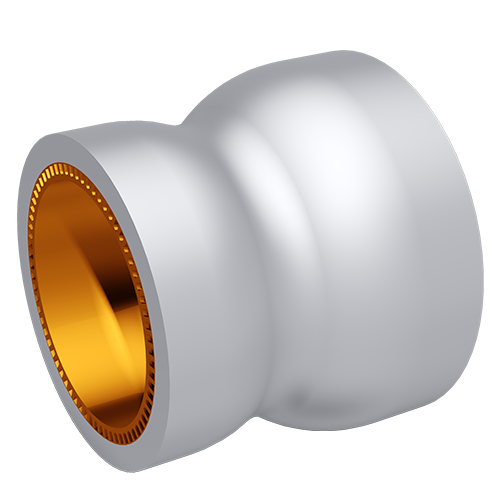
Removing the mandrel
In the subsequent phase, the mandrel is eliminated through machining or chemical dissolution. The filler material within the channels is then extracted using chemical etching in water or acidic/alkaline water solutions, resulting in the formation of unobstructed channels for the circulation of the cooling medium.

Combustion chamber liner demonstrator
- High strength Cu-alloy combustion chamber demonstrator
- Weight ~20 kg
- Length 300 mm
- Diameter approx. 300 mm

Demo with cold sprayed jacket material
- High thermal conductive & high strength Cu alloy
- Al support outer diameter 250 mm
- Approx. 25 kg Cu alloy
- 18 mm coating thickness
- Jacket material cold spray deposition: ~15 kg stainless steel
Applications
From the frying pan to space technology - the spectrum of possible applications is huge.
References
Renowned companies from all over the world have trusted the Impact Spray systems for years.