Benefits of Additive Manufacturing
with Cold Spray

Cold Spray Additive Manufacturing is a highly-efficient process to build freeform components and structures at high deposition rates. Since the metal powder is neither fused nor melted during the cold spray process, heat related distortion can be avoided and a protective atmosphere is not required.
- Immense deposition rates
- Possibility to deposit nearly all metals and alloys
- Possibility to combine dissimilar materials (bimetallics)
- Nearly unlimited build-up dimensions
- High density, homogeneous coatings with superior adhesion
- High deposition efficiency rates (up to 100%)
- Great thermal and electrical conductivity (no oxides or thermal barriers)
- Environmentally friendly process (no toxic waste, low energy consumption)
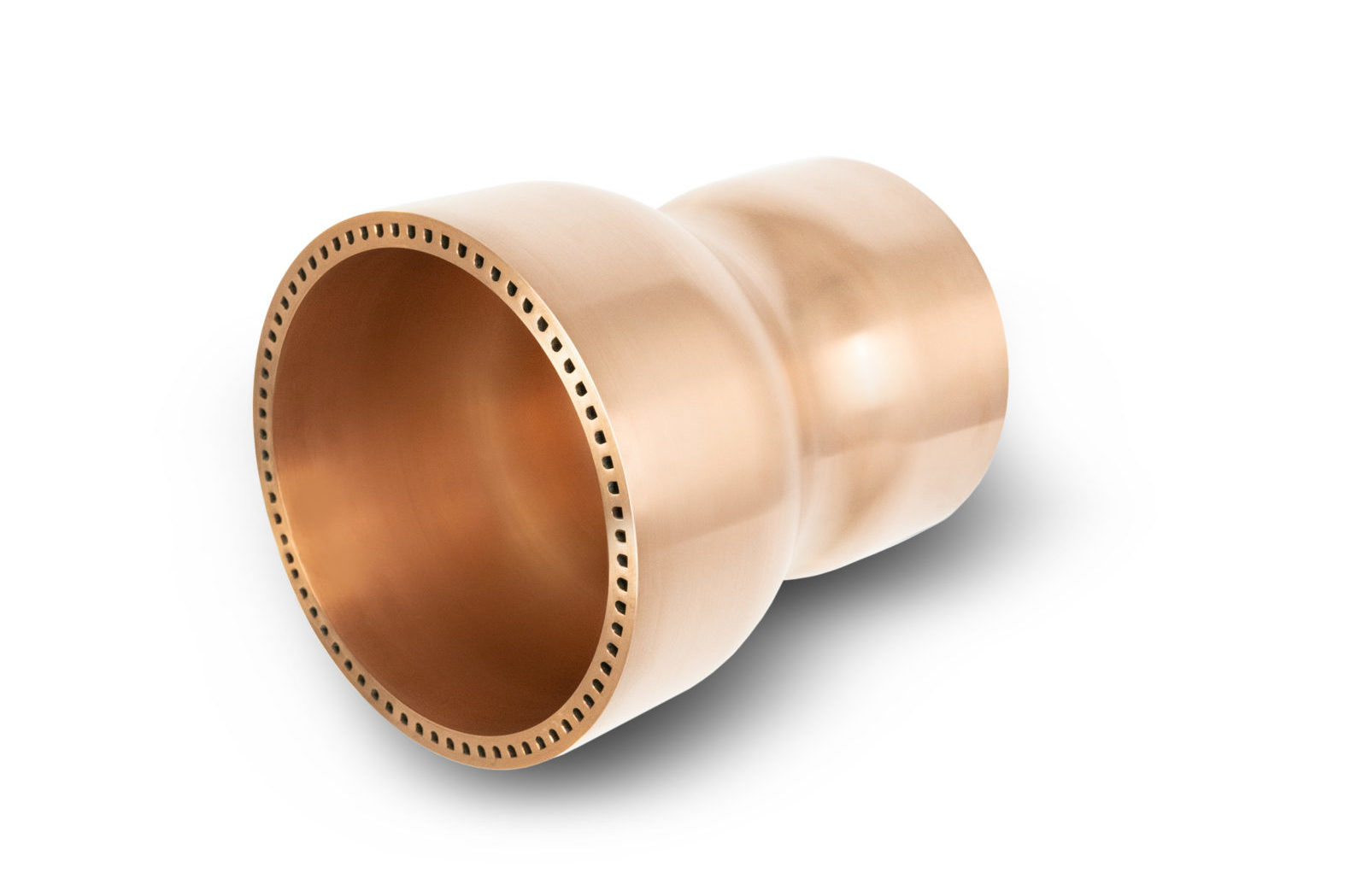
Cold Sprayed Combustion Chamber

Additive manufacturing complex parts for the space industry by using cold spray allows not only unlimited dimensions and the combination of different materials, but also a massive reduction of the manufacturing time and costs.
Rotation symmetrical casing components

The combination of a conventionally produced components with additive manufactured elements reduces the production time of rotation symmetrical casing components significantly.
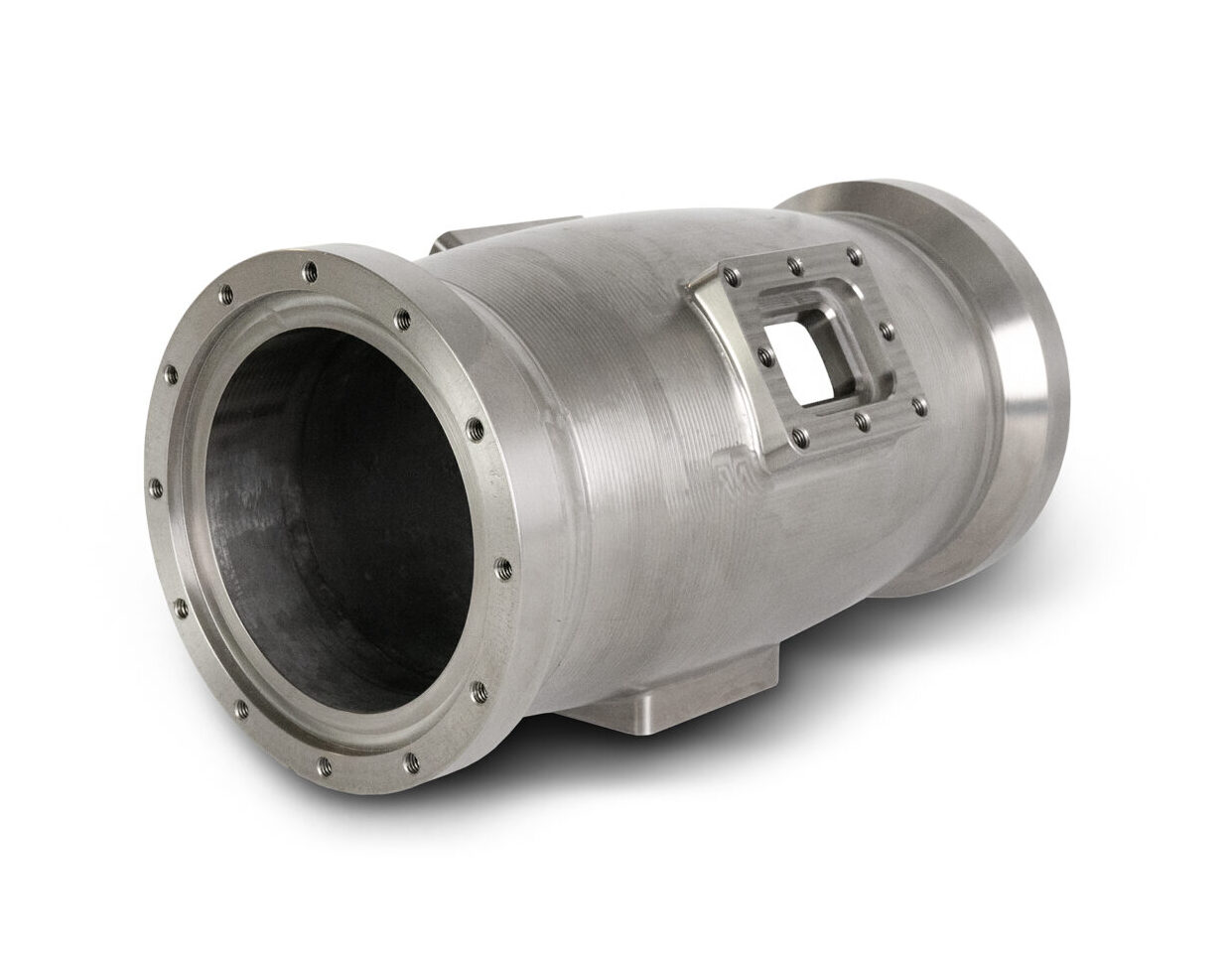
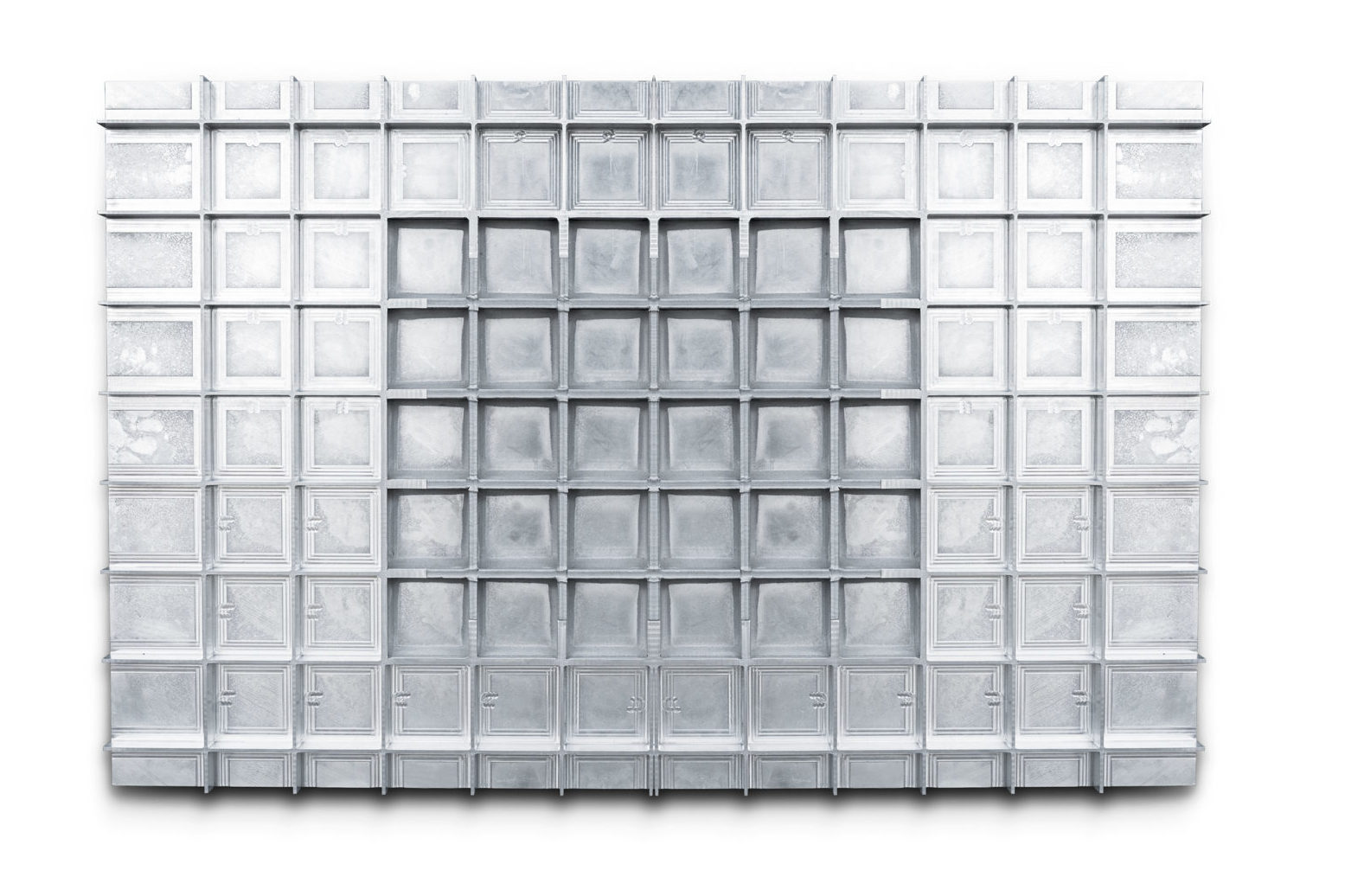
Cold Sprayed Orthogrid Structure

Cold Spray Additive Manufacturing orthogrids, mainly used in aerospace, allows material savings up to 70% in comparison to the conventional production methods.
Never miss any cold spray news!
Receive helpful tips about additive manufacturing and coating with cold spray. Also be the first to be informed about the latest cold spray equipment and new technological progresses.