LINSPRAY® Connect: Delivering the next generation of Cold Spraying
Developed in collaboration between Linde and Impact Innovations, LINSPRAY Connect is a smart, reliable and safe gas supply solution that gives manufacturers more insight and control over their cold spray process.
Mourning Peter Richter

The perfect combination:
Impact Hybrid Brake Disc Coating®
With Impact Hybrid BDC® we combine two worlds of technology in one brake disc coating: The strong metallurgical connection of a laser-deposited intermediate layer with a crack- and corrosion-resistant cold gas top layer...
The new Impact Angle Head Gun with axial injection
Over a development period of almost 4 years, both our own considerations for product optimization and feedback from customers and partners have flowed into this new cold gas spray gun Impact Gun 6/11 AH EvoCSII. The result is an innovative cold spray gun that has unique features and benefits.


For download: Presentation by Leo Holzgaßner at the chassis.tech plus
The Co-CEO, Technical Director and Co-Founder of Impact Innovations, Leonhard Holzgaßner gave a presentation at chassis.tech plus 2023 entitled "Particle emission reduction for brake discs via high-performance Cold Spray Coating". You can download this presentation as a PDF here.
Cold spray for inner diameter coatings and their properties
Due to recent developments, cold gas spraying technology can now be used to create inner diameter coatings for cylinder inner diameters > 70 mm. The present investigations focus on the process optimization and the specific properties of cold gas spray inner diameter coatings created with three different alloy steel powder variants.

Cold spray additive manufacturing
At the moment, the main limitation of CSAM is the generally low ductility of the as-sprayed deposits. In this scientific paper, using Cu as a model material, we demonstrate a way to overcome this limitation. We show that without any post-heat treatment, the properties of CSAM Cu are comparable to bulk, non-AM Cu.
CSAM-Process for Ti-6Al-4V using N2 as propelling gas
The Cold Spray Additive Manufacturing technology is particularly attractive for the manufacturing of large parts, which are challenging for today's powder bed fusion-based 3D printing processes due to equipment size limitations or protective atmosphere necessity, especially when depositing reactive materials such as Ti-6-4.

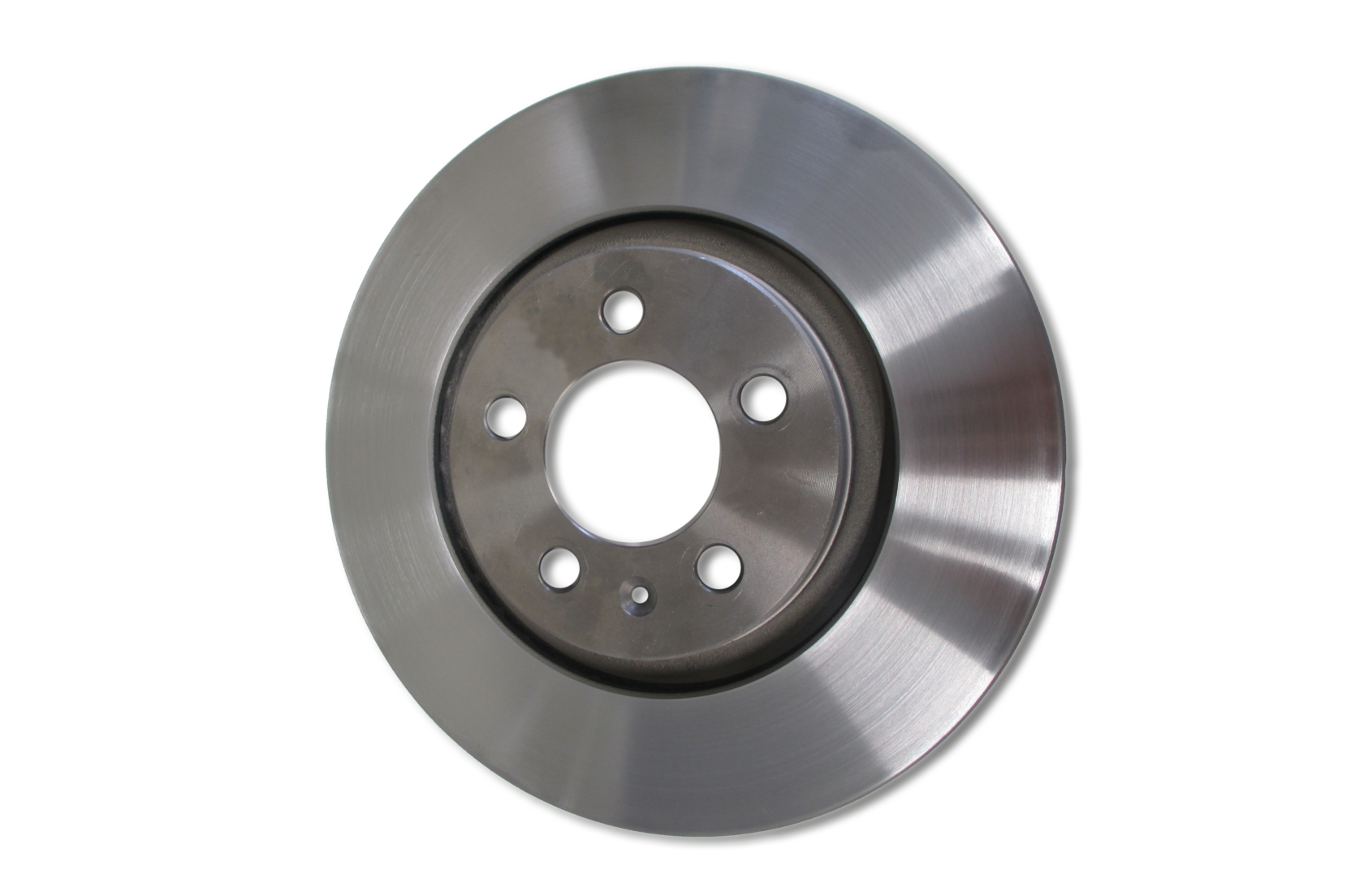
High-performance cold gas coating for brake discs
Emissions from brake wear, such as brake dust and particulate matter, are a growing concern for the automotive industry. As gray iron remains the most commonly used brake disc material for vehicles, cold gas coating of gray iron break discs is a viable solution.
Cold Spray Additive Manufactured Combustion Chamber
Impact Innovations set up a collaborative project with Airborne Engineering (AEL), a UK based company specializing in a propulsion system design and testing. AEL designed a combustion chamber demonstrator according to Impact Innovations guidelines. The regeneratively cooled liner is a high-strength Cu-alloy, and the outer jacket material is Inconel. You can find out more about this in our press release, which you can download here.

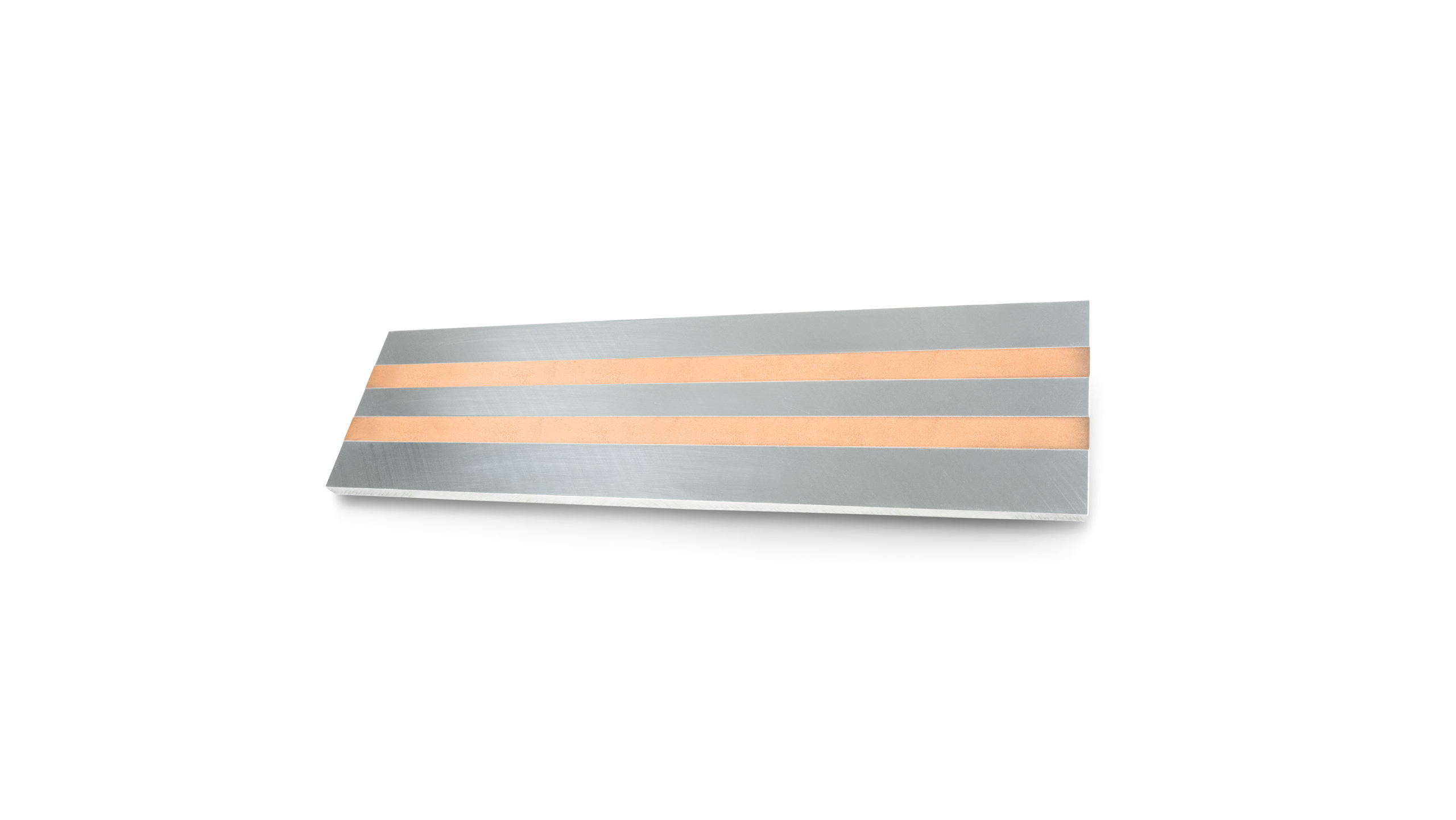
Copper Coated Aluminum Busbars
Impact Innovations' cold spray system presents an exciting alternative that allows the replacement of copper busbars with aluminum and combines the thermal benefits of copper with lightweight aluminum.
Flexible solution to apply ID coatings
When using the Rotating ID Coating Device for cold gas spraying of coatings with an inner diameter, greater flexibility is achieved and energy consumption is reduced.


Cold Sprayed Hybrid Heatsinks
Hybrid heatsinks combine the thermal conductivity of copper with the advantages of aluminium.
The latest generation of Impact Cold Spray Systems
The new Impact Cold Spray System EvoCSII is great for serial production. Thanks to a higher number of sensors, data recording and an integration in higher-level controlling, the process reliability is increased significantly.

We expand and triple the company building
For the symbolic groundbreaking ceremony for the new building in Rattenkirchen, the management of Impact Innovations GmbH met with Mayor Rainer Greilmeier and architect Thomas Elger. After an intensive planning phase, construction work is now starting on the new company building in the industrial area in Rattenkirchen. The new building will be connected directly to the existing building and the production area will more than tripled.

In addition, a new office building with spacious social and office space is being built on a usable area of 680 m². The completion of the new building is planned for mid-2021.
Impact Innovations currently employs almost 30 people, and the number is set to increase with the new building: "We initiated a new growth phase last year and want to pursue and promote this despite the challenges of the current situation." says the management of Impact Innovations.
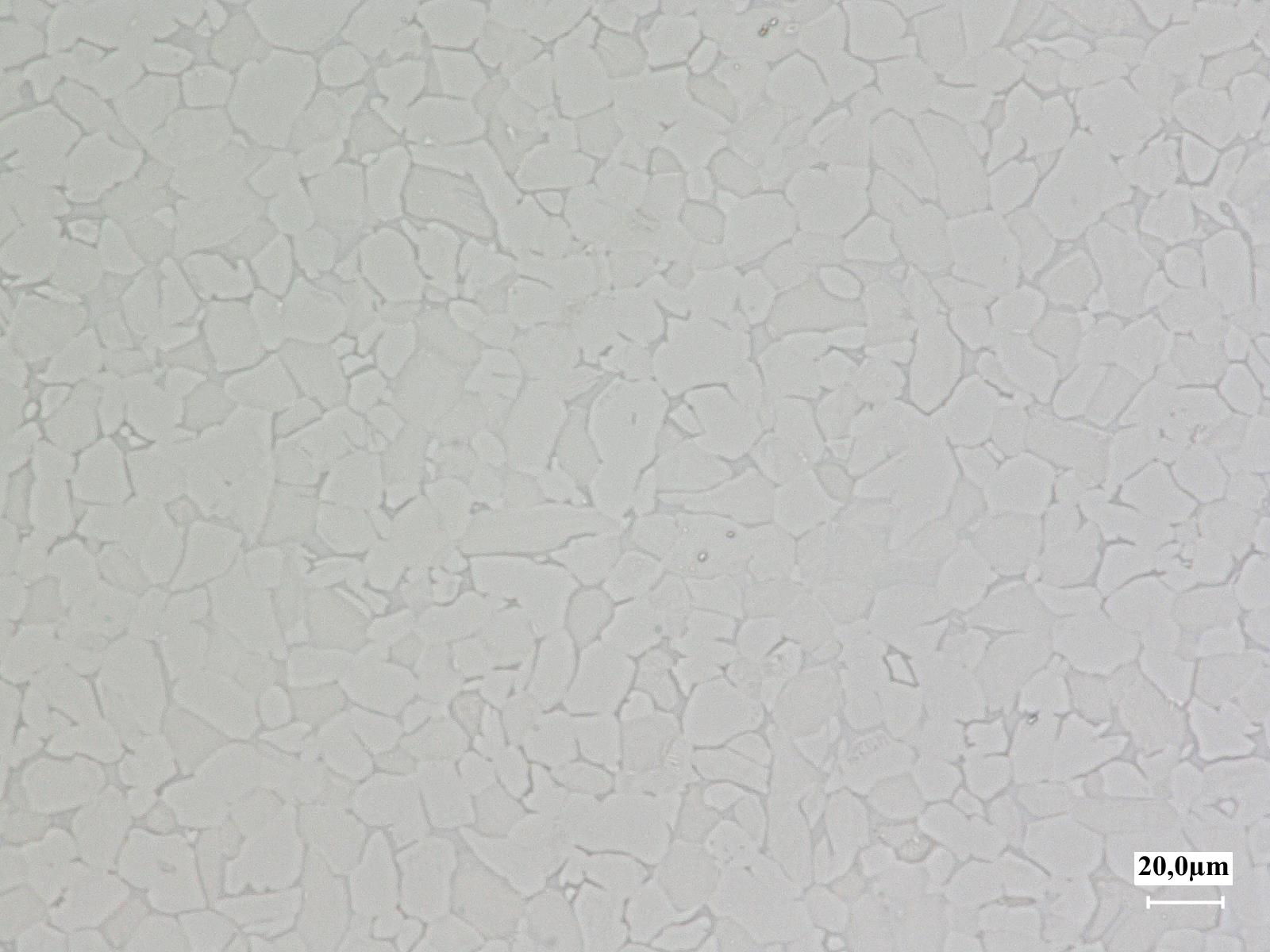
Cold Spraying Ti-6Al-4V
Impact Innovations has developed the Cold Spray Additive Manufacturing process for Ti-6Al-4V using nitrogen as propelling gas.
Finalists for the René Wasserman Award
Impact Innovations was nominated for the René Wasserman Award. The award was created by Christopher Wasserman in memory of his father René Wasserman, who is regarded as a pioneer in welding technology and thermal spraying.
In late summer 2020, we welcomed Prof. Dr.-Ing. Kirsten Bobzin and Werner Krömmer in our headquarter. They are executive board members of the 'Gemeinschaft Thermisches Spritzen e.V. ' and form the René Wasserman Award’s jury together with Christopher Wasserman. It is an honor to be one of this year's finalists! Congratulations to the winner!
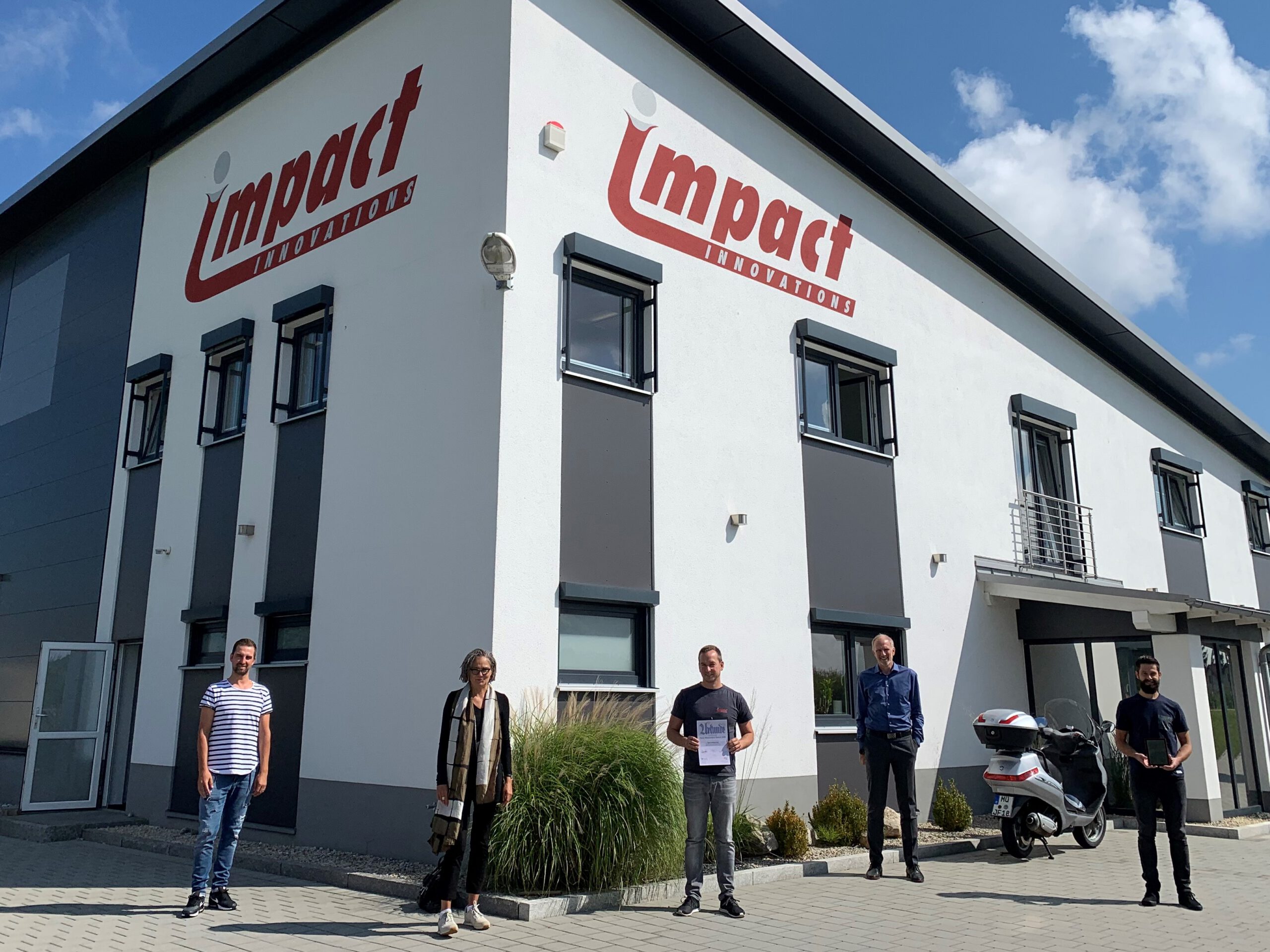
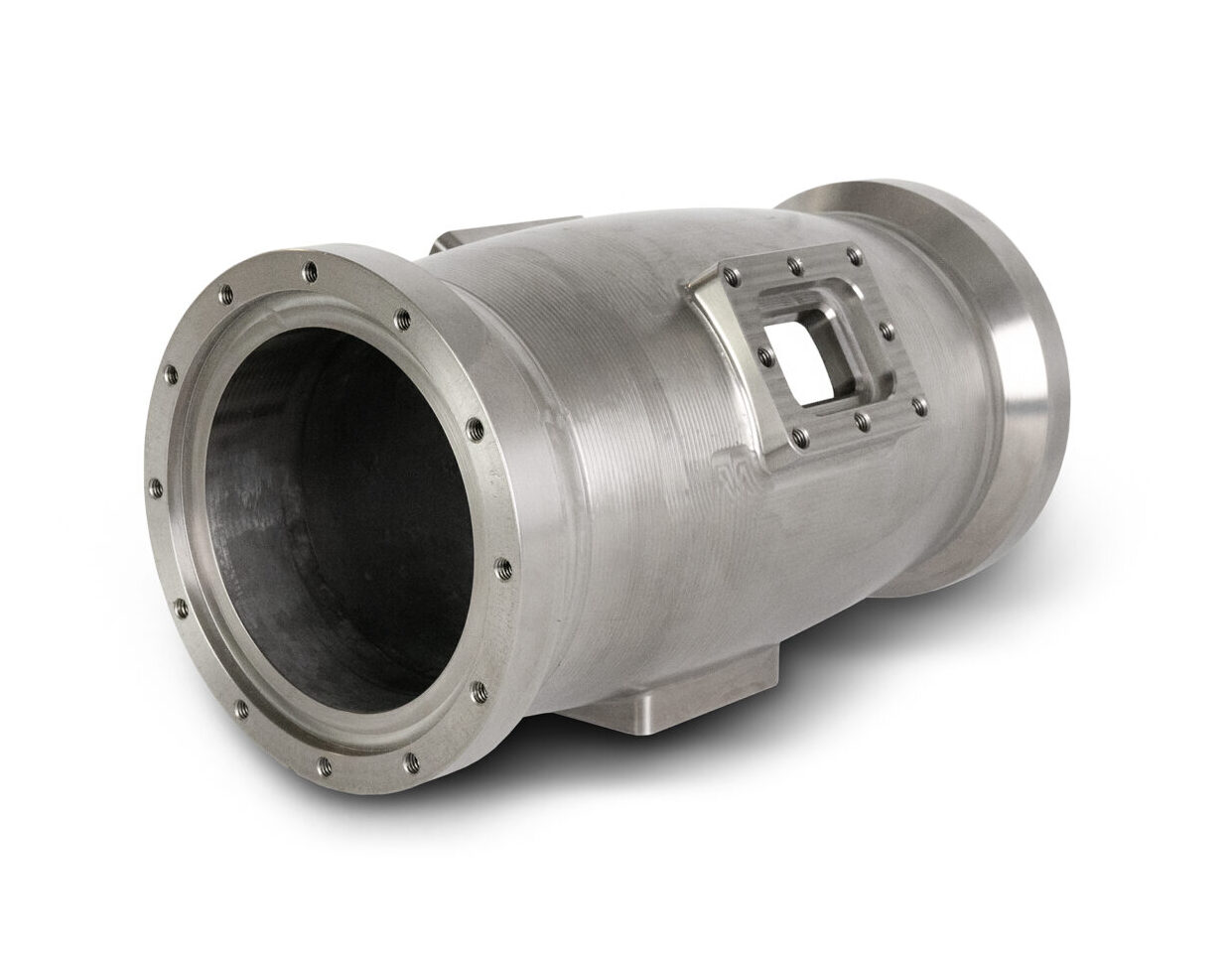
Additive Manufacturing with Cold Spray
Cold Spray Additive Manufacturing offers outstanding mechanical properties, large dimensions and specific geometrical complexity. To demonstrate the potential of the CSAM process as an innovative process for additive manufacturing, we created an overwiew with possible applications.
New team member
We are delighted to introduce Dr.-Ing. Sascha Bernhardt as Head of Sales at Impact Innovations. He is responsible for building a strong operating sales team and for pushing our sales to the next level by establishing the cold spray technology as a widespread industrial manufacturing process. Thanks to his valuable experience and his in-depth knowledge, we were able to gain a highly qualified colleague.
Sascha Bernhardt already held various management positions in international sales at medium-sized technology companies and acts according to the motto: If you don't try, you'll never succeed.
He is enthusiastic to start working with the skilled and dynamic Impact team. His target is to support Impact customers gaining a competitive edge by introducing the capabilities of the cold spray technology.
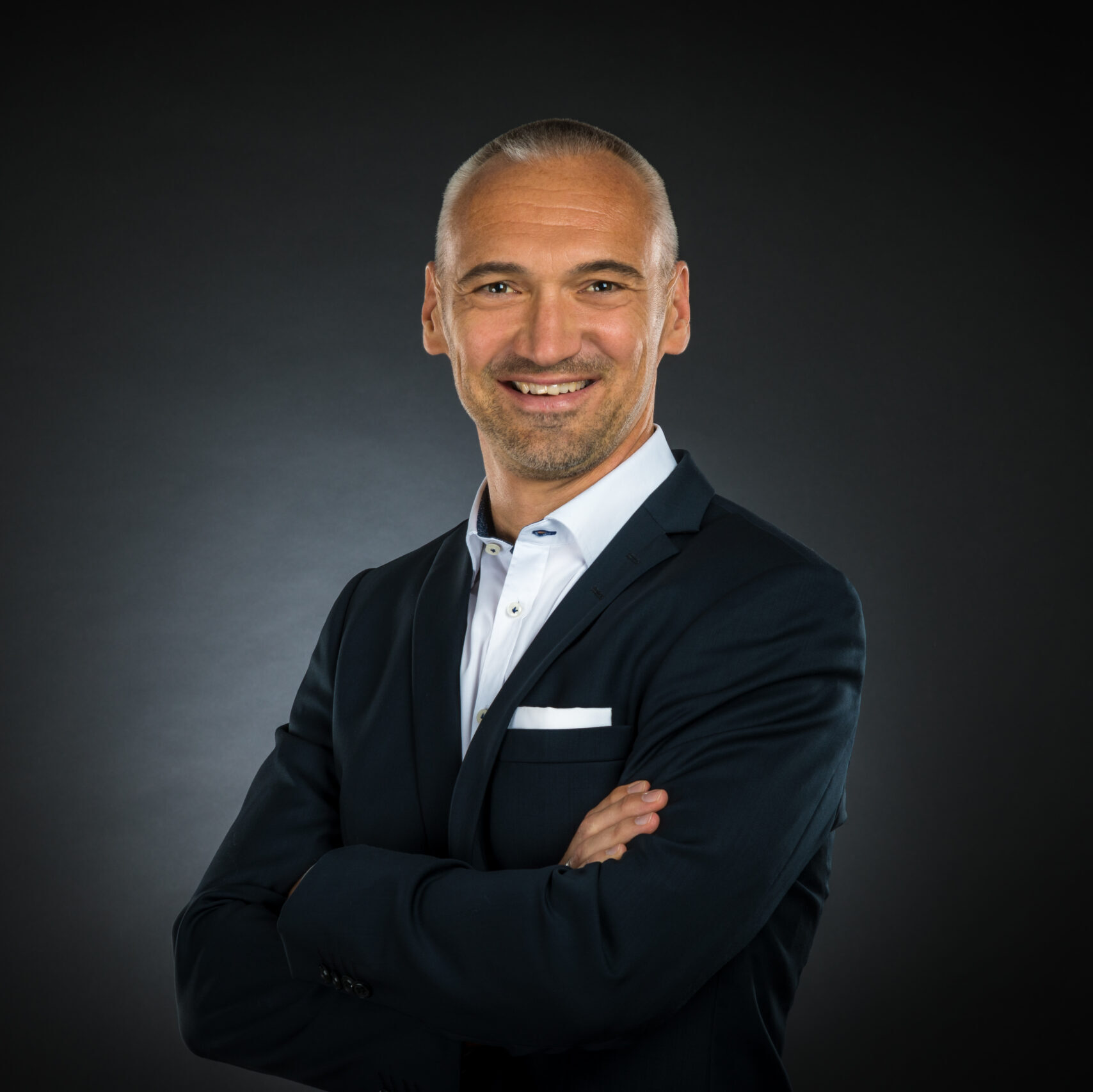
Dr.-Ing. Sascha Bernhardt
Head of Sales
Never miss any cold spray news!
Receive helpful tips about additive manufacturing and coating with cold spray. Also be the first to be informed about the latest cold spray equipment and new technological progresses.